Services We Provide
At Pro Appliance Repair, we recognize the significance of a properly operating freezer in your home. Whether it’s preserving perishables, keeping ice cream at the perfect consistency, or chilling beverages for a gathering, a malfunctioning freezer can throw off your household rhythm. That’s where we step in.
Backed by years of hands-on experience and specialized knowledge, our team of licensed technicians is committed to delivering swift and dependable freezer repair solutions.
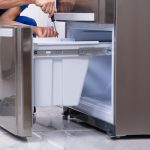
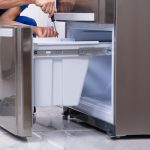
Diagnostic Assessment
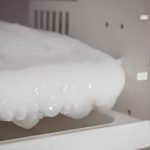
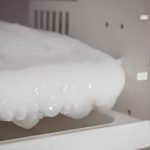
Defrost System Repair
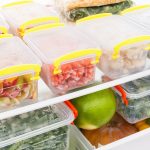
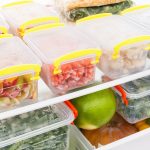
Compressor Replacement
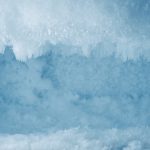
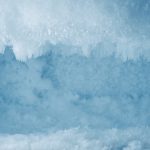
Temperature Calibration
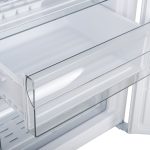
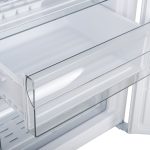
Condenser Coil Cleaning
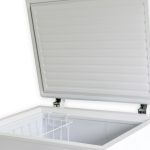
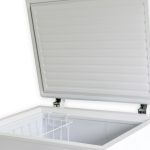
Door Seal Replacement
Frequently Asked Questions
If you notice any of the following signs, it’s likely time to consider freezer repair: inconsistent temperature inside the freezer, excessive frost buildup, strange noises like buzzing or knocking, leaks of water or coolant, or if the freezer fails to maintain a consistently cold temperature.
Water leaks from a freezer can be caused by various factors, including a clogged defrost drain, a malfunctioning water inlet valve, or a damaged door seal. It’s essential to identify the source of the leak and address it promptly to prevent water damage and potential mold growth.
The duration of freezer repair depends on factors such as the complexity of the issue, the availability of replacement parts, and the technician’s schedule. While some repairs can be completed within a few hours, others may take longer, particularly if specialized parts need to be ordered.
Yes, we stand behind the quality of our workmanship. We provide warranties on both parts and labor for added peace of mind. Please inquire about specific warranty terms for your repair.
Yes, several preventive maintenance steps can help extend the lifespan of your freezer. These include cleaning the condenser coils regularly, ensuring proper ventilation around the appliance, avoiding overloading the freezer, checking and replacing door seals if damaged, and scheduling regular professional maintenance checks to detect and address any potential issues early on.